TECHNOLOGY
STRUTO is a Nonwoven structure where all the fibers are orientated in the vertical position; this gives the highest possible resilience and recovery after repeated compression.
STRUTO is a technically engineered structure with the following properties;
- Lightweight
- Consistent
- Recyclable
- Support
- Resilient
- Recovery
- Absorption
The STRUTO Vertical Lapping process can use most fibers that are properly blended with a Bi Component fiber. Once blended and carded the Vertical Lapping process creates a very even finish product. The STRUTO Vertical Lapper can be retro fitted after most Nonwoven blending and carding systems.
STRUTO Vertical Lapped Nonwoven structures are very successful in a number of fields such as OEM Automotive component manufacturing. STRUTO is commonly used in this field as a replacement for bulky heavyweight cross laid and air laid insulation materials, headliner, floor and trunk systems. Horizontal fiber orientation is shown below.
The most effective way to achieve the maximum amount of resilience, compression resistance and recovery is with a Vertical fiber orientation. STRUTO is truly a Vertically Lapped fiber orientation as opposed to a horizontally laid fiber orientation. The purpose of the STRUTO system is to make the most resilient structure possible with the least amount of fiber when compared to other structures.

In any Nonwoven process the fibers must be opened prior to blending. Once properly blended the fibers are carded. The carded web is conveyed up an incline apron and is fed into the STRUTO Lapping device. The Vertical Lapper then folds the web into a uniform structure. The folds are compressed together into a continuous STRUTO structure, the structure is held in a Vertical position as it enters the heated Thermal Bonding Oven. Once the structure has been Thermally Bonded, it enters the cooling zone causing the Thermally Bonded structure to become permanent.
A typical STRUTO process line will begin with fiber Blending, Opening, Pre Carding, Cross Lapping, Finish Carding, STRUTO Vertical Lapper, Thermal Bond Oven, Cooling Zone, Slitting, Cutting, Winding, Reclaim System and Electrical Controls.
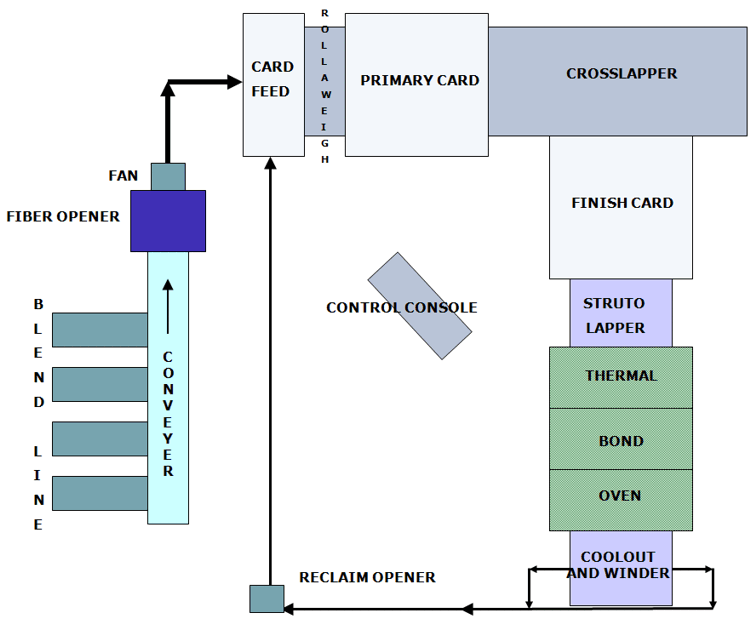
STRUTO PARAMETERS
The minimum height of a STRUTO product is approximate 15 mm depending on the fiber type and density of the finished product.
The maximum height of a STRUTO product is approximately 40 mm depending on the fiber type and density of the finished product.
STUTO products can be slit horizontally depending on product density and the amount of binder fiber in use. This does not include very lightweight, lofty or soft structures.
The minimum density which can be achieved with a STRUTO structure is approximately 120/150 grams per square meter or 3 ½ ounce per square yard.
The maximum density which n be achieved with a STRUTO structure is approximately 1600 grams square meter or 45 ounce per square yard at the 25 mm or 1 inch thickness.
All parameters are based upon the use of standard 6 to 15 denier, 52 to 64 mm, mechanically crimped, virgin polyester fibers. STRUTO structure are commonly produced with the use of all types of fibers such as Kevlar, Nomex, Glass, Carbon Fibers as well as all types of natural fibers such as Jute, Cotton, Flax and Kenaf.
STRUTO is able to provide complete Turn Key installation from the engineering phase to training your staff to produce a quality STRUTO Vertically Lapped Nonwoven product.
The staff here at STRUTO would be happy to run product samples on one of our Lab lines.
|